The most common reason for increased surface friction is stent retention. If a stent detaches during transit to the deployment site it can cause serious complications to a procedure. In order to prevent this from happening, the surface friction can be controlled using different types of balloon materials.
Each balloon material has a different coefficient that affects the surface friction of the balloon. Materials with low coefficients include: PET, nylon, and high durometer PEBAs. Alternatively, materials with high coefficients include low durometer PEBAs, and low durometer Urethane. If a balloon has a low coefficient of friction it will take more compressive force to attain the same static holding force. The coefficient of friction for low durometer urethanes is 3.5X higher than PET. As a result, the holding force will also be 3.5X higher with the same compressive load. To achieve high burst pressures with high surface friction a multilayer construction is recommended. The inner layer in this design would be PET, nylon, or high durometer PEBA and the outer layer would be a low durometer PEBA or low durometer urethane. Once blow molded the wall thickness of the outer layer can be reduced to .0003” to .0004” providing little impact to profile but provide significant increase in surface friction.
An alternative way to increase surface friction is by increasing the surface area. The use of texturing on the balloon can improve the surface friction. Improved surface friction occurs when features have square edges. If the surface features look like domes, they will provide little improvement. If the surface features look like pillars, they will provide improved surface friction.
The issue with pillar shaped surface features is blow molding pressures and temperatures are too low to create the square edges. The result of a pillar feature in a mold is dome shaped. The loss of shape retention is a result of air trapped in those voids which even at extremely high pressures will still leave a small gap at the edges. Additionally, the material is not molten so it will not flow. There will always be an elastic element to the material and in combination with high stress concentrations in those corners the material will shrink and try and return to their pre blown state after removed from the heat and pressure. Other more exotic methods of impart texturing is needed to improve surface friction.
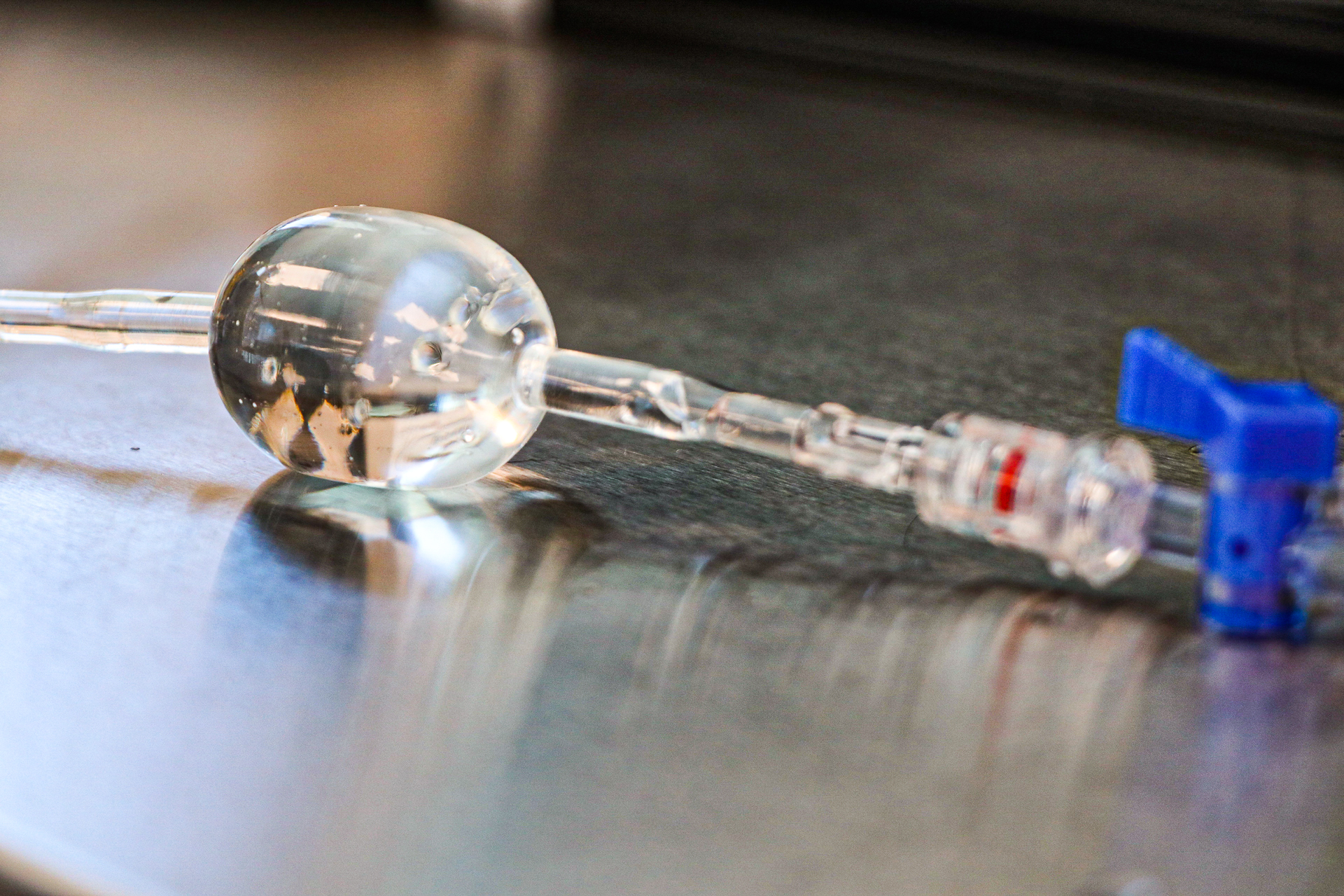